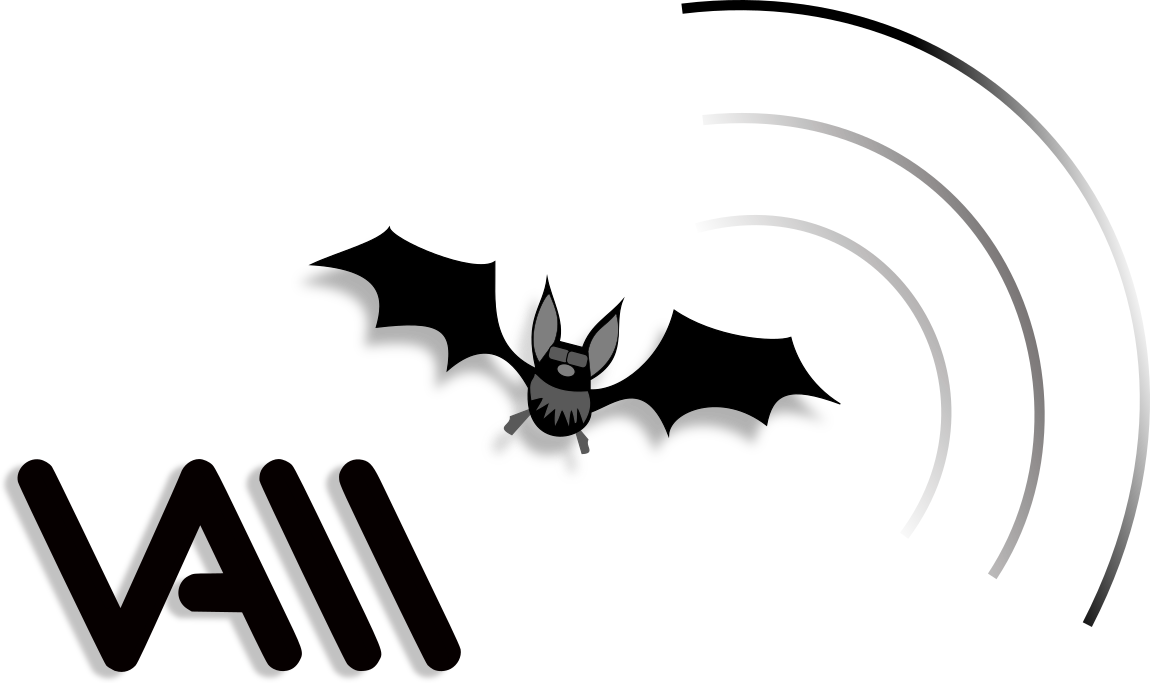
VIBROAKUSTISCHES
MONITORING
ZUR STRUKTUR-, PROZESS- UND MASCHINENÜBERWACHUNG
Startseite » Vibroakustisches Monitoring
Vibroakustisches Monitoring
Mit Fledermausohren
In der Ära von Digitalisierung und Industrie 4.0 sind intelligente Überwachungssysteme, gestützt auf hochleistungsfähige Sensornetzwerke und maßgeschneiderte Modelle, entscheidend, um die gesamte Wertschöpfungskette in Echtzeit zu steuern und zu optimieren.
Unser vibroakustisches Monitoringsystem (VAM) hört mit Fledermausohren auf Ihre wertvollsten Prozesse und informiert Sie bei Abweichungen vom Normalzustand.
Lieber vorher hinhören als später teuer bezahlen!
AMITRONICS Gmbh
MobileS Monitoring System
Entdecken Sie unsere flexible, mobile Zustandsüberwachung mit Fokus auf Acoustic Emission. Unsere hochsensible Messtechnik erfasst präzise extrem kurze Schallereignisse im Bereich von Millionstel Sekunden. Dank fortschrittlicher Echtzeit-Signalverarbeitung kann diese Technologie nahtlos in Ihre Infrastruktur integriert oder über unsere hausinterne Cloud-Technologie autonom betrieben werden.
Wir zeichnen uns durch mühelose Anpassbarkeit mit anwendungsspezifischen Schnittstellen und benutzerfreundlichen Dashboards aus, um rasch auf neue Herausforderungen und Problemstellungen reagieren zu können. Nutzen Sie unsere mobile Zustandsüberwachung, um präzise und flexible Lösungen in Ihrer Branche zu realisieren.
Vorteile unserer Technologie:
- Zerstörungsfreier Einsatz von AE-Sensoren
- Autark dank LTE und/oder batteriebetrieben
- Hohe Empfindlichkeit der AE-Sensoren erlaubt größere Abstände vom Schallentstehungsort
- Unterstützung bei der Integration in Ihre spezifische IT-Infrastruktur mit vielen Schnittstellen (TCP/UDP, MQTT, OPC-UA,…)
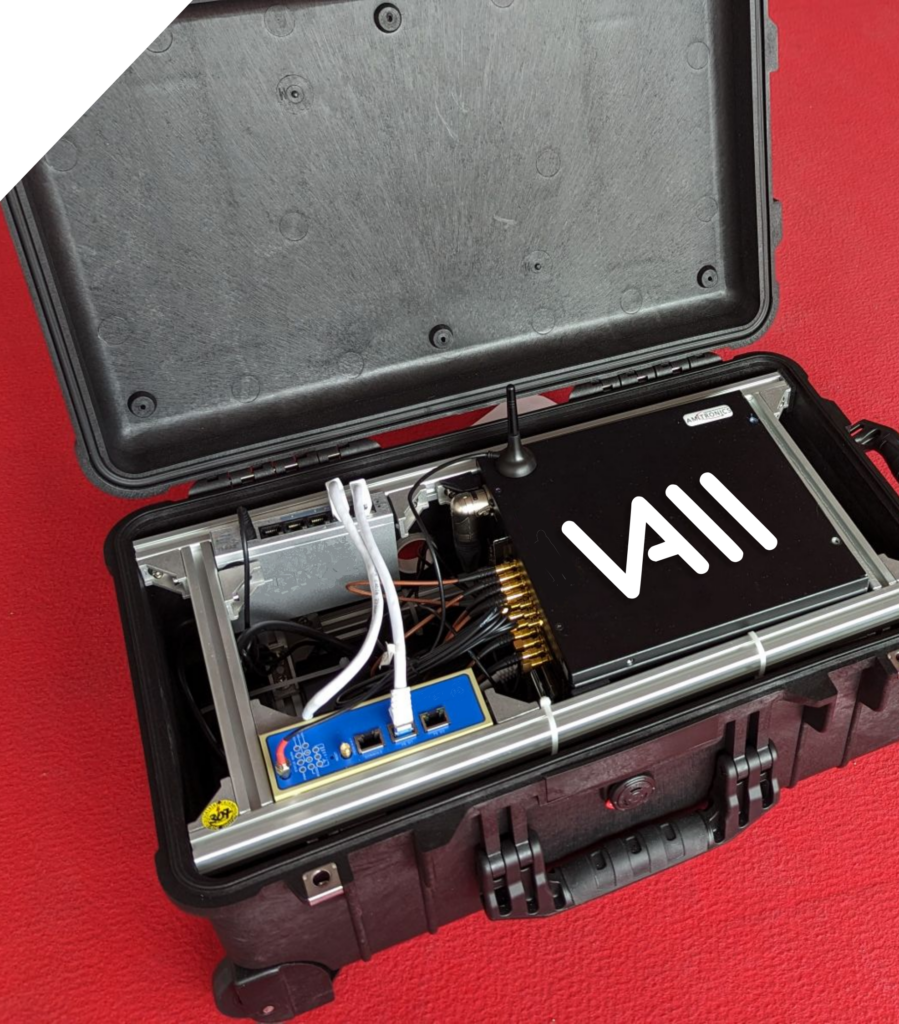
Anwendungsfälle der Zustandsüberwachung
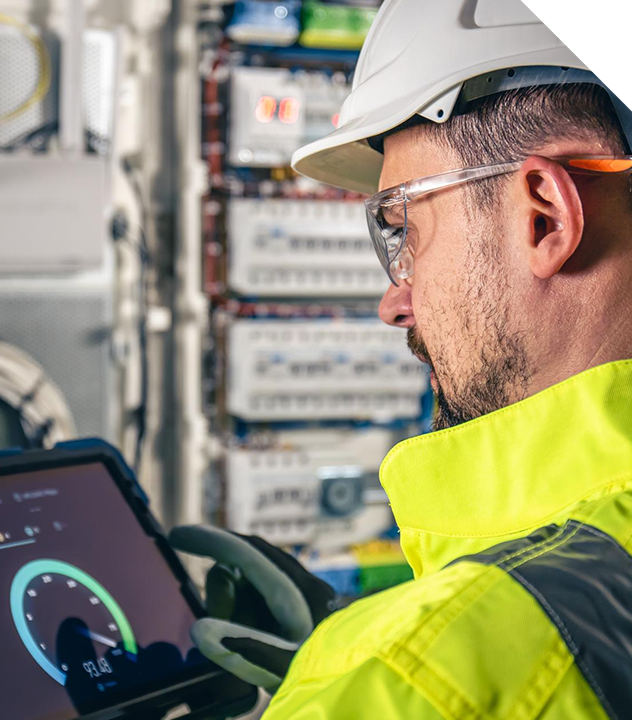
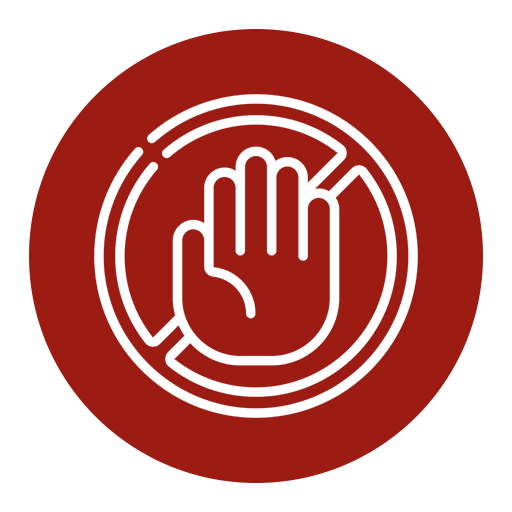
Produktqualität
- Ziel: Identifikation von Strukturschäden
- Erkennung, Lokalisierung und Klassifizierung von inneren (unsichtbaren) Schädigungen
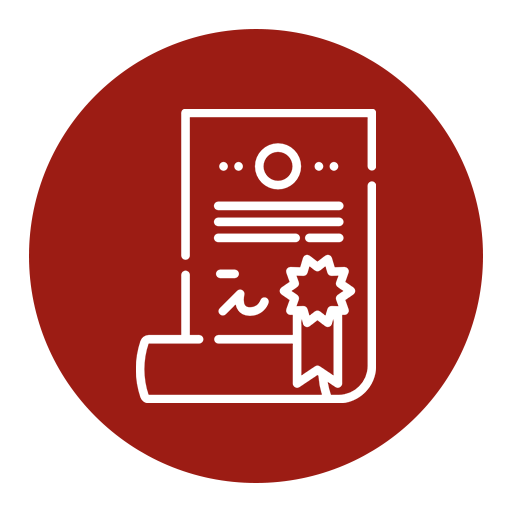
Maschinenzustandsanalyse
- Ziel: Sicherheit und Funktionalität der Maschine/Anlage
- Überwachung der Maschinenstruktur
- Verschleiß/Schäden erkennen, z.B. durch Trendanalysen
- Vermeidung von Ausfällen durch frühzeitige Diagnose („Predictive Maintenance“)
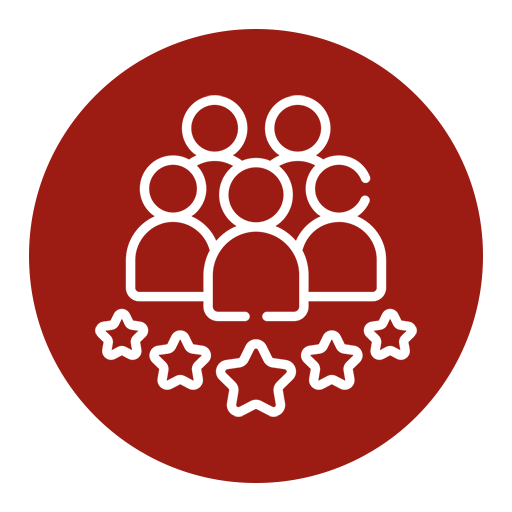
Prozessüberwachung
- Ziel: Steigerung der Prozessqualität und Maschineneffizienz
- Analyse von Prozessänderungen
- Detektion von Prozessstörungen in Echtzeit
- Online-Qualitätsüberwachung der Bauteile
Vibroakustisches Condition Monitoring
Bisherige Anwendungen
und Forschungsinhalte
Akustische Fehlerbilder werden von erfahrenen Maschinenbedienern oft als Rattern, Klappern, Knarzen oder Quietschen beschrieben. Neben den hörbaren Klangmustern gibt es auch solche, die durch unsere Analysen im Ultraschall sichtbar werden. Der erfahrene Maschinenbediener erkennt diese Klangmuster und kann diesen, auch im Kontext vieler anderer Geräuschquellen, Fehlerbilder zuordnen. Die AMITRONICS arbeitet daran, diese Fehlerbilder durch sensorische Intelligenz in Algorithmen abzubilden. Dazu werden die aufgenommenen Körperschalldaten direkt analysiert, Quellen getrennt und relevante Merkmale extrahiert. Auf Basis dieser reduzierten Merkmale kann sich der Algorithmus schnell auf neue Prozesse einlernen, um Anomalien und Prozessfehler zu detektieren. Ziel ist es, auf Basis der Zustandsinformationen die Prozessgrenzen stärker auszureizen, die Bauteilqualität zu überwachen und Maschinen- und Werkzeugausfälle frühzeitig zu erkennen. In gezielten Forschungsprojekten treiben wir die Technologie in unterschiedlichen Anwendungsbereichen voran und automatisieren verschiedene sonst aufwendige Prozesse.
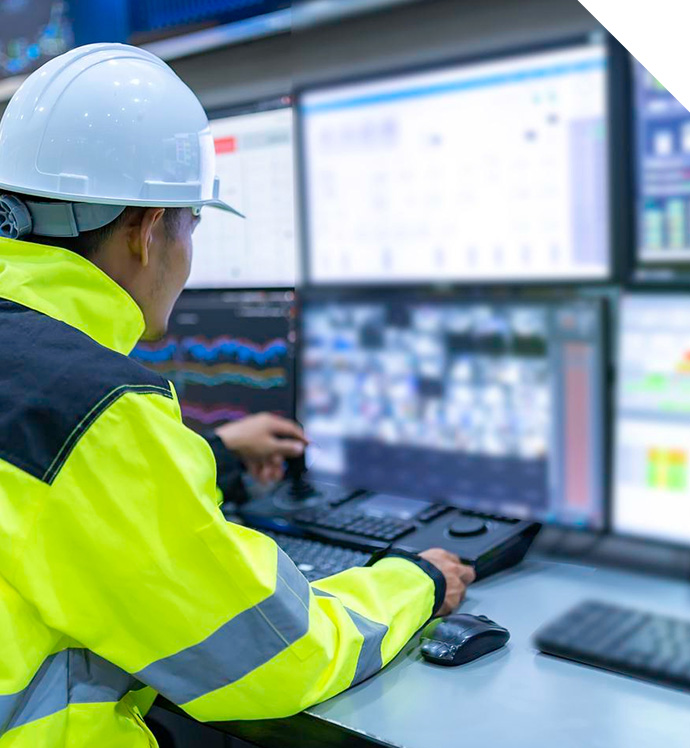
AMITRONICS Gmbh
Anwendungen
Überwachung Von Gebäuden, Bauwerken, Brücken, und Baustellen
Ultraschallschweißen, Laserschweißen, Biegen, Schleifen
Drucktanks, Leckagen in Leitungen
Textilvliesherstellung und Anwendungen der Papierindustrie
Amitronics Gmbh
Forschungsprojekte
HZwo-Inspect VIBRA. Modularer Prüf- und Charakterisierungsbaukasten zur Herstellung von Brennstoffzellen und Elektrolyseuren
Ministerium: BMWK (03EN5033F)
Laufzeit: 01.04.2023 – 31.03.2026
AE-DigiScale. Innovatives-System zur Skalierung und Optimierung von Acoustic Emission IOT-Systemen durch einen digitalen Zwilling
Ministerium: BMWK (EP201616)
Laufzeit: 01.11.2024 – 31.10.2027
INTEUM. Intelligentes, echtzeit- und transferfähiges System für Predictive Maintenance und Qualitätsüberwachung gespeist aus Produktionsplanungs- und Maschinenüberwachungsdaten
Förderprogramm: Elektronische Systeme
Projektträger: VDI/VDE-IT (DIE-2108-0006//DIE0156/01)
Laufzeit: 31.10.2024 erfolgreich abgeschlossen
PANAMERA. Entwicklung eines Predictive Maintenance Baukastens für automotive Applikationen mittels Fahrzeug-Flottenanalyse
Ministerium: BMWK (19I21016B)
Laufzeit: 30.09.2024 erfolgreich abgeschlossen

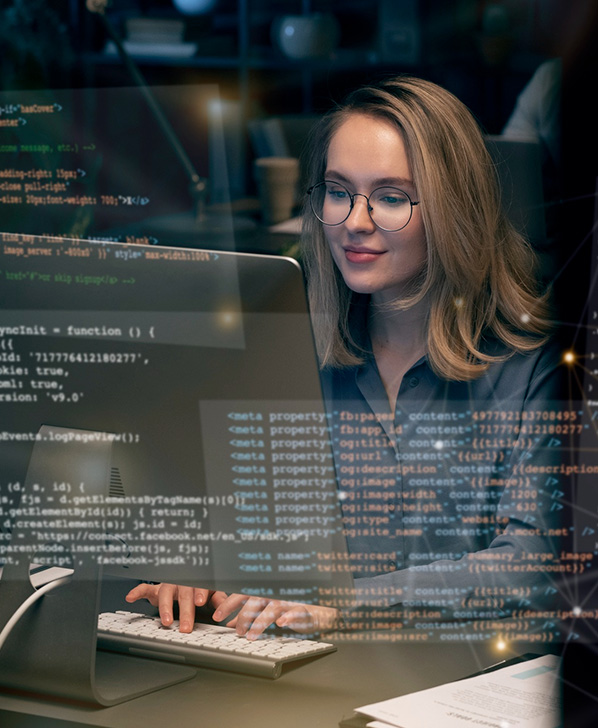
Amitronics GmbH
Unsere Vorgehensweise
Erstanalyse
Konzeption, Auswahl und Platzierung der Sensorik
Messdatenerfassung, Analyse und Zuordnung
von Signalinhalten mit Ihrem Fachpersonal
Nachbereitung der Messdaten
Berechnung von Merkmalen und
Mustererkennung
Erste Ergebnisdiskussion bereits am Versuchsobjekt
Dauerlauf
Mustererkennung in verschiedenen Entwicklungsschritten
Anwendung und Entwicklung von Analyseverfahren zur Merkmalsgewinnung
Neuronale Netze und Deep Learning zur Anomalieerkennung
Flexible Netzwerk-Kommunikation z.B. mit der Maschinensteuerung
Live-Dashboard zur Zustandsüberwachung und Entwicklung von interaktiven Mensch/Maschine-Schnittstellen
FAQ
Ist vibroakustisches Monitoring für meine Anwendung geeignet?
- Art der Anwendung: Vibroakustisches Monitoring mit Acoustic Emission Sensoren wird häufig in der strukturellen Überwachung, der Materialprüfung und der Qualitätskontrolle eingesetzt.
- Art des Materials oder der Struktur: Diese Technik ist besonders nützlich, um Risse, Brüche, Spannungskonzentrationen und ähnliche strukturelle Probleme in Materialien wie Metall, Glas, Beton oder Verbundwerkstoffen zu überwachen.
- Ziele der Überwachung: Klären Sie, welche Informationen Sie durch das Monitoring gewinnen möchten. Acoustic Emission Sensoren können Schäden frühzeitig erkennen, aber auch Schwingungs- und Geräuschdaten liefern.
- Umgebungsbedingungen: Einige Anwendungen erfordern spezielle Sensoren, die extremen Temperaturen, Druck oder anderen Umweltbelastungen standhalten können. Die Sensoren sind zwar klein, müssen aber montierbar sein.
- Kosten und Ressourcen: Dauerüberwachung mit Acoustic-Emission Sensoren und hohen Datenraten ist nicht vergleichbar mit den typischen niederfrequenten Sensoren. Bietet für wertschöpfende Prozesse allerdings sehr hohes Einsparpotential. Die Lebensdauer von bestehender Werkezuge, oder Infrastruktur zu erhöhen ist zudem sehr nachhaltig.
Kann vibroakustisches Monitoring auch ohne Cloudanbindung eingesetzt werden?
Selbstverständlich! Unser Monitoring-System kann auch ohne Cloudanbindung verwendet werden. In der Regel verwenden wir die Cloudanbindung hauptsächlich im Kontext von Dauerläufen. Für Kunden, die sich für unsere Serviceleistungen entscheiden, bieten wir die Möglichkeit, die Übertragungsdaten und das Zeitfenster flexibel anzupassen. Wir stellen berechnete Features für weiterführende Aufgaben im lokalen Netzwerk bereit, dabei sind verschiedene Übertragungsprotokolle wie MQTT und OPC-UA möglich. Die Integration kann flexibel an die notwendigen Bedürfnisse angepasst werden.
Was ist Acoustic Emission überhaupt? Warum keine Beschleunigungsaufnehmer?
Acoustic Emission (AE) ist eine Technik zur Erkennung und Analyse von elastischen Wellen, die bei der Deformation oder dem Versagen von Materialien und Strukturen erzeugt werden. Diese Wellen entstehen aufgrund von Mikrorissen, Rissausbreitung oder anderen strukturellen Veränderungen und können als akustische Signale erkannt werden. Acoustic Emission wird oft in der zerstörungsfreien Prüfung eingesetzt, um Anzeichen von Materialermüdung, Rissbildung oder anderen strukturellen Problemen in Bauteilen oder Anlagen frühzeitig zu erkennen.
Warum keine Beschleunigungsaufnehmer? Beschleunigungsaufnehmer sind Sensoren, die dazu verwendet werden, Beschleunigungen in einem bestimmten Bereich zu messen. Sie sind nützlich, um Vibrationen und Erschütterungen zu erfassen. Während Beschleunigungsaufnehmer in vielen Anwendungen wie der Vibrationsüberwachung oder der Fahrzeugdiagnose verwendet werden, sind sie in Bezug auf die Erkennung von Mikrorissen oder Rissausbreitung in Materialien weniger empfindlich als Acoustic Emission-Sensoren.
Die Wahl zwischen den beiden hängt von den spezifischen Anforderungen der jeweiligen Anwendung ab.
Welche Vorteile hat die Acoustic Emission gegenüber Kameratechnologie?
Acoustic Emission (AE) bietet einige Vorteile gegenüber Kameras in bestimmten Anwendungen:
Nicht visuelle Erkennung: AE erfasst akustische Signale, die von strukturellen Veränderungen oder Rissbildungen in Materialien erzeugt werden. Dies ermöglicht die Erkennung von Ereignissen, die visuell nicht sichtbar sind, wie Mikrorisse oder Rissausbreitung im Inneren von Materialien.
Früherkennung: AE kann Anzeichen von Materialermüdung oder strukturellen Problemen in einem frühen Stadium erkennen, bevor visuelle Anzeichen oder sichtbare Schäden auftreten. Dies ermöglicht eine proaktive Wartung und Schadensprävention.
Echtzeitüberwachung: AE ermöglicht die kontinuierliche Echtzeitüberwachung von Strukturen und Materialien. Dies ist besonders wichtig in sicherheitskritischen Anwendungen wie dem Bauwesen, der Luft- und Raumfahrt oder der Öl- und Gasindustrie.
Nicht-invasiv: Im Gegensatz zu Kameras erfordert AE keine direkte Sichtlinie auf das zu überwachende Objekt. Es kann in geschlossenen Umgebungen, unter Wasser oder in schwer zugänglichen Bereichen eingesetzt werden.
Empfindlichkeit: AE-Sensoren sind empfindlich für akustische Signale, selbst wenn sie in einem lauten Umfeld auftreten. Dies ermöglicht die Erkennung von subtilen akustischen Veränderungen.
Langzeitüberwachung: AE kann über längere Zeiträume hinweg kontinuierlich eingesetzt werden, ohne dass eine ständige visuelle Überwachung erforderlich ist.
Es ist jedoch wichtig zu beachten, dass die Wahl zwischen Acoustic Emission und Kameras von den spezifischen Anforderungen der jeweiligen Anwendung abhängt. In einigen Fällen, insbesondere in visuell orientierten Anwendungen, wie der Überwachung von Produktionsprozessen oder der Videoüberwachung, sind Kameras möglicherweise die bessere Wahl. In anderen Fällen, in denen nicht sichtbare strukturelle Veränderungen oder Materialermüdung von Bedeutung sind, kann Acoustic Emission eine wertvolle Ergänzung oder Alternative sein.
Wie funktioniert der Datenschutz und die IT-Sicherheit beim vibroakustischen Monitoring?
- TISAX-Zertifizierung: Das Unternehmen ist TISAX (Trusted Information Security Assessment Exchange) zertifiziert. TISAX ist ein etablierter Standard in der Automobilindustrie, der sicherstellt, dass Unternehmen angemessene Maßnahmen zur Gewährleistung der Informationssicherheit getroffen haben. Diese Zertifizierung zeigt unser Engagement für hohe Sicherheitsstandards.
- Verschlüsselte und anonymisierte Übertragung notwendiger Daten: Alle übertragenen Daten, insbesondere sensible Informationen, werden verschlüsselt übertragen. Dies stellt sicher, dass die Daten während der Übertragung vor unbefugtem Zugriff geschützt sind. Darüber hinaus werden Merkmalsdaten anonymisiert und komprimiert übertragen um die Nutzbarkeit auf die Aufgabe zu beschränken.
- Effiziente, komprimierte Speicherung der Daten in hauseigener Cloudinfrastruktur in Deutschland: Die Daten werden in einer Cloudinfrastruktur der AMITRONICS gespeichert, die sich in Deutschland befindet. Dies gewährleistet, dass die Daten in einem Land mit strengen Datenschutzgesetzen und -vorschriften gespeichert werden. Die effiziente und komprimierte Speicherung ermöglicht eine Platzersparnis und trägt zur Kosteneffizienz bei, ohne die Sicherheit zu gefährden.
Predictive Maintenance was bedeutet das überhaupt?
Predictive Maintenance ist eine Schlüsselkomponente der Industrie 4.0, die es ermöglicht, den Zustand von Maschinen und Anlagen vorherzusagen und vorbeugende Wartungsmaßnahmen durchzuführen, um Ausfälle zu vermeiden.
Die Grundlage von Predictive Maintenance bildet die automatisierte kontinuierliche Erfassung und Sammlung von Maschinendaten durch Sensoren und Überwachungssysteme. Diese Daten werden analysiert, um potenzielle Probleme zu erkennen, wobei verschiedene Analysetechniken wie maschinelles Lernen und Künstliche Intelligenz zum Einsatz kommen.
Die Vorteile von Predictive Maintenance sind vielfältig: Sie ermöglicht gezielte und automatisierte Wartungsmaßnahmen, minimiert Ausfallzeiten und Reparaturkosten, verbessert die Anlagenverfügbarkeit und steigert die Effizienz, Produktivität und Rentabilität. Im Vergleich zur reaktiven oder präventiven Wartung zeichnet sich Predictive Maintenance durch eine datengetriebene, vorausschauende und bedarfsgerechte Wartung auf Basis von Echtzeitdaten aus.